We had one essential task today to be able to launch Tornseglare as booked on Friday: properly attach the rudder to the boat. And a long list of nice-to-haves we hoped to manage. But we bareeeeeely managed, with much frustration including a fall into a patch of stinging nettle, as well as some creativity and humor, to complete the essential.
The first night we slept on our boat last summer we were kept awake by a constant banging sound. Eventually, with our friend Peter’s help, we determined the sound was the bolt holding the rudder to the boat banging about in its sleeve.
“Put a new bushing in there when you have it up on land,” advised Peter.
At that point it sounded intimidating. When and how were we getting the boat on land? And what was a bushing anyway? (It’s a plastic cylinder!)
Well today, we have re-installed the rudder with not one but two new bushings, one above and one below, and holy hell was it a nightmare.
All our focus had been on the bushing we could (eventually) see- that attached the rudder to the back of the boat. We eventually found Maxispecialisten who was able to send us the parts -“both upper and lower.” We had no idea what that meant at first. The upper one required a lot of hand sanding to shorten it enough to fit between the two metal plates. We tested that first thing today and high fived excitedly when it fit. But reader, our troubles had just begun.
We confidently pounded in the bushing in the lower fitting on the bottom of the hole of the boat. But now when we tried to fit in the rudder, it just would not go. There was about a centimetre off for the top to fit in where it needed to be bolted. And this is what took three hours to fix.
Measuring the angle and depth, sanding the inside with everything we could find to thin out the bushing. The crazy thing was everything looked and measured like it should work fine. It was definitely deep enough and the width also looked correct so why didn’t it fit?!?!?
We tried a lot of things including a rather ingenious pulley system to pull the rudder up from the boat from under the tiller bolt, so the person below could really force it up, but it wasn’t enough. Eventually we realised that there was a sliiiight problem with the angle the bushing had been pounded in, which seemed to bend slightly partway up (too far in to feel with our fingers but from a lot of messing about with a long bolt that was the conclusion). Which meant the pin was hitting the bushing and getting stuck. It was impossible to get the bushing out again from this one-way tube without breaking it. So Simon wrapped a bolt in sandpaper and sanded hundreds of times by hand while I told him Hans Christian Andersen stories from my favorite ride at Tivoli. On approximately the 17th try, it worked!!!
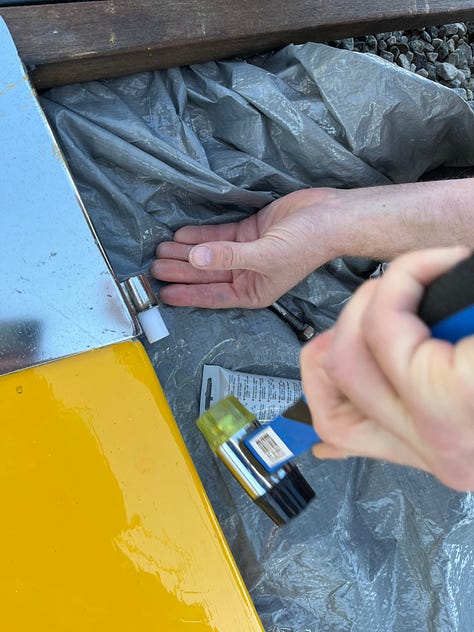
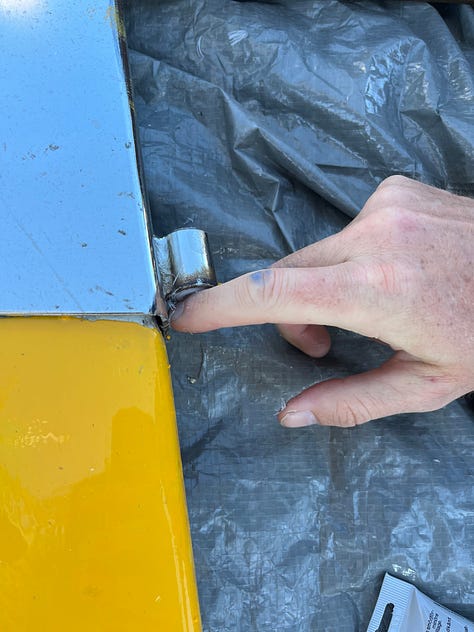
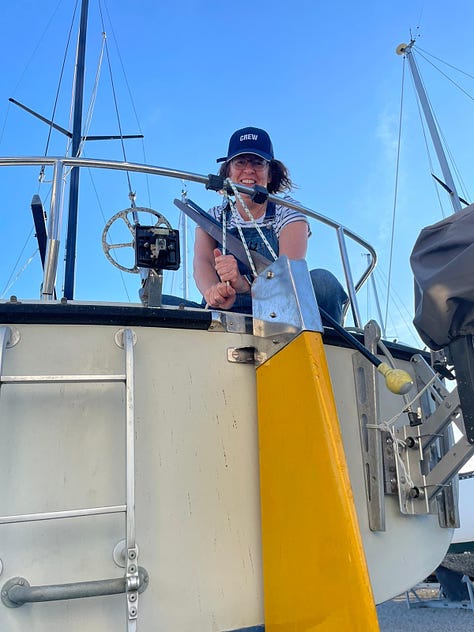
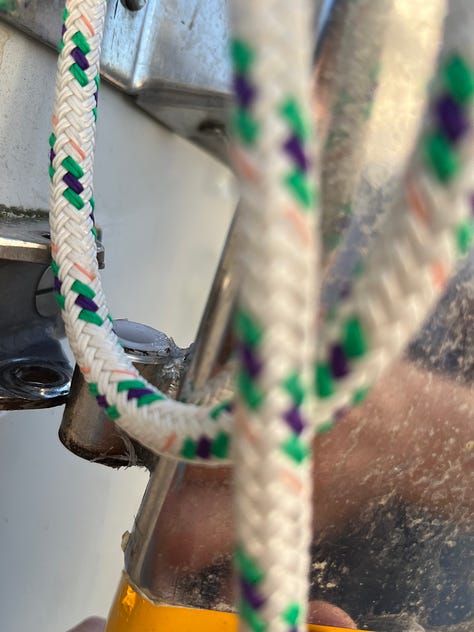
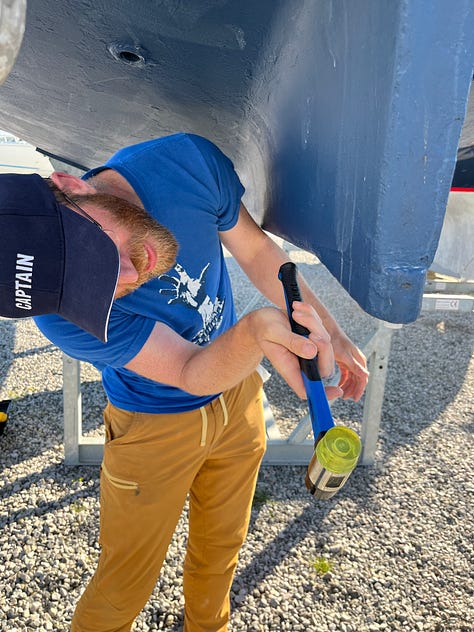
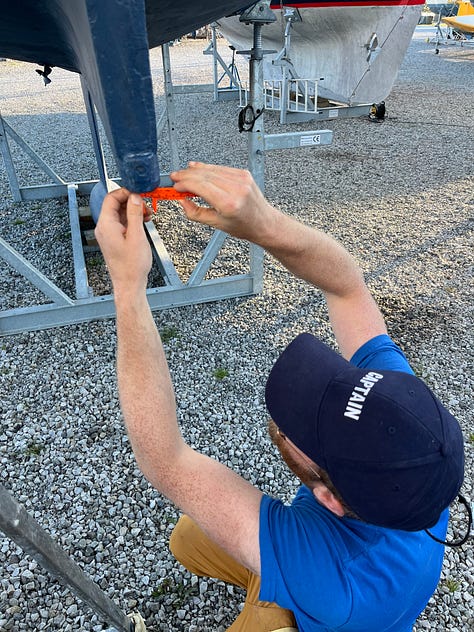
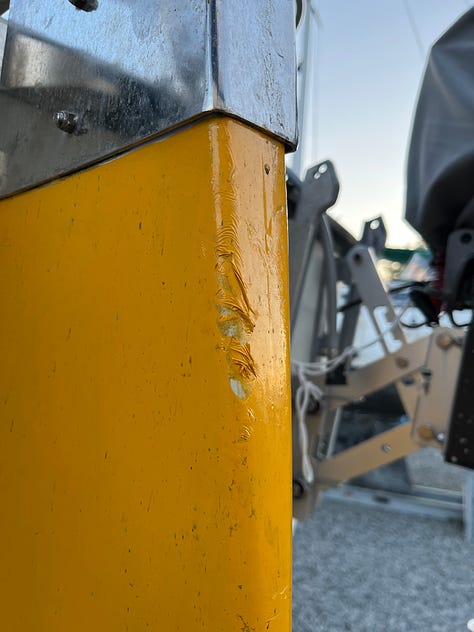
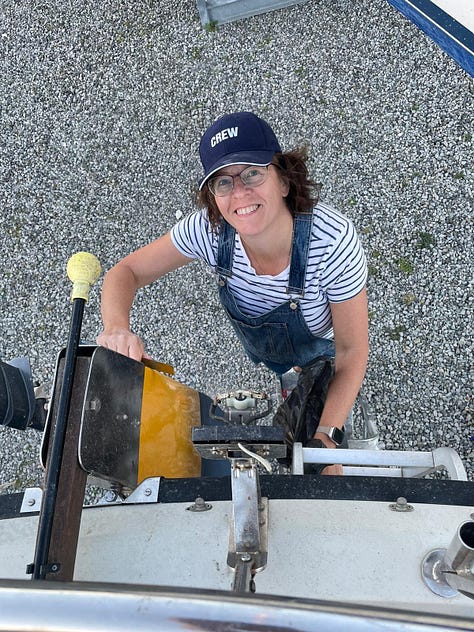
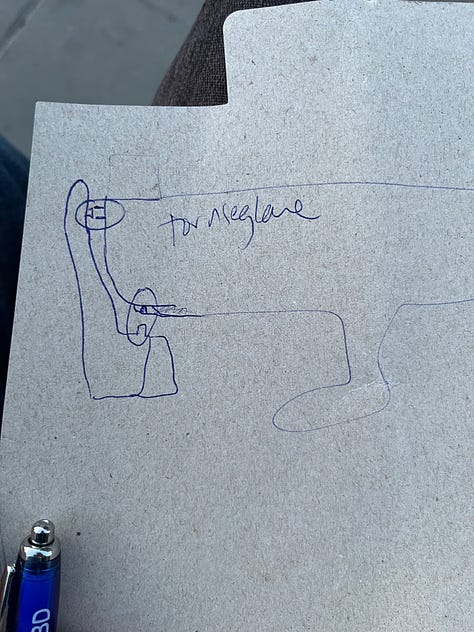
We also noticed the pretty yellow paint we applied to the rudder was still tacky in places 3 days later! :( Must have glopped it on too thick we scraped off the tacky parts and will try to slap a quick coat on with rollers before launch Friday.
lessons learned:
Think thru all parts of a job before you commit.
Test things in systems - maybe we should have tried just the upper bushing and just the lower bushing before both were in place.
Rollers apply paint smoother than brushes.
The bushing story made me laugh... Been there done that. The funny thing is... There is often a simpler way to do things...only to be discovered far too late to be helpful lol. Boat Life.